
Lithium Battery Pack Assembly Process
Description
The manufacturing process of Lithium Battery Pack involves multiple complex and critical steps,which are detailed below:
1.Raw material inspection
Strictly inspect raw materials such as lithium battery cells,connectors (usually copper or nickel),battery management systems (BMS),casing materials,insulation materials,etc,for example,checking whether the capacity,voltage,internal resistance and other parameters of lithium battery cells meet the requirements;check the material purity and dimensional accuracy of the connecting piece;check the functional integrity and stability of BMS.
2.Battery cell sift
To ensure the consistency and performance stability of lithium battery packs,it is necessary to screen a large number of lithium battery cells,classify battery cells based on their capacity,voltage,internal resistance,and other parameters,and select battery cells with similar performance for the manufacture of the same battery pack.
3.Battery Pack assembly
3.1 Connection method selection
According to the design requirements,connect the selected lithium battery cells in series,parallel,or series parallel,common connection methods include welding (such as laser welding, ultrasonic welding) and mechanical connection (such as bolt connection),laser welding can achieve efficient and precise connections,with high welding strength and low resistance;mechanical connections facilitate disassembly and maintenance.
3.2 Connection operation
Taking laser welding as an example, the connecting piece is accurately placed on the positive and negative poles of the battery unit,and the connecting piece and battery pole ears are instantly melted by the laser beam to form a firm electrical connection. During the welding process, it is necessary to strictly control welding parameters such as laser power, welding time,welding speed,etc,to ensure welding quality.
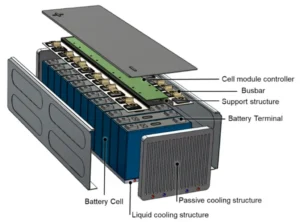
4.Install Battery Management System (BMS)
4.1 BMS function
BMS is the core control component of lithium battery pack,which has functions such as monitoring battery status (such as voltage, current, temperature),charge and discharge control, overcharge and over discharge protection, balance management, etc.
4.2 Installation connection
Install the BMS module to the designated location of the battery pack and connect it to each battery unit and external interface through wires,the connection process should ensure that the wires are firmly connected and well insulated to avoid problems such as short circuits or poor contact.
5.Install cooling system (optional)
5.1 Determination of heat dissipation requirements
For high-power,high-capacity,or temperature sensitive lithium battery packs,a heat dissipation system needs to be installed to ensure that the battery operates within a suitable temperature range.
5.2 Cooling methods and installation
Common cooling methods include air cooling and liquid cooling,the air cooling system installs cooling fans and ventilation channels to allow air to flow and remove heat;the liquid cooling system requires the installation of coolant pipes and heat sinks,the coolant circulates in the pipes,transferring heat to the heat sinks and dissipating it.
6.Insulation treatment
Inside the battery pack, insulation materials (such as insulation paper, insulation tape, etc.) are used to isolate the battery cells,connecting pieces,BMS and other components to prevent short circuits,ensure that the coverage area of the insulation material is complete and tightly adhered.
7.Shell packaging
1.According to the design requirements and application scenarios of lithium battery packs,choose suitable shell materials such as plastic, metal,etc,process the selected shell material to have appropriate size and shape,while reserving installation holes, interfaces,and other positions.
2.Place the assembled battery units, BMS, and cooling system components into the processed casing for fixation and positioning,then use sealant or sealing gasket to seal the outer shell, preventing dust, moisture,etc,from entering the interior of the battery pack and affecting battery performance and safety.
8.Testing and Quality Control
8.1 Electrical performance testing
Conduct comprehensive electrical performance testing on the packaged lithium battery pack,including measuring parameters such as open circuit voltage,internal resistance,and capacity,as well as conducting charge and discharge characteristic tests to ensure that the performance of the battery pack meets design requirements.
8.2 Security performance testing
Conduct a series of rigorous safety performance tests, such as overcharge protection test,over discharge protection test, short circuit protection test, needle puncture test, extrusion test, hot box test,etc,these tests aim to simulate the operational status of lithium battery packs under various extreme conditions and verify their safety performance.
8.3 Aging test
The lithium battery pack that has passed the electrical and safety performance tests will undergo aging testing,through a certain number of charge and discharge cycles,the performance of the battery pack will be more stable, and potential unqualified products will be further screened out.
9.Quality inspection and traceability
Conduct quality testing and record keeping for each lithium battery pack,and establish a comprehensive quality traceability system,once product quality issues are discovered,they can be traced back to information such as raw material suppliers,production processes,and operators through records,in order to take timely improvement measures.
10.Packaging and Storage
For lithium battery packs that have passed all tests and inspections,customized packaging boxes are usually used, and product information such as brand,model,specifications,rated voltage,rated capacity, etc,are marked on the packaging boxes,then store the packaged lithium battery pack in the warehouse and wait for shipment.